

Ø Number and location of radiographic shall minimum as specified on API Standard 650, Section 6. Ø Inspection by radiographic method is not required for roof-plate or bottom-plate welds, for welds joining roof plates to top angle, the top angle to the shell plates, shell plates to bottom plates, or appurtenances to tanks. Ø Radiographic inspection is required for shell butt weld, annular-plate butt welds, and flush-type connection with butt welds. Ø Radiographic examination method shall be in accordance with the ASME section V, Article 2. Ø Vacuum box tested using a test pressure at least 3 psi gauge or as specified on Company specification.
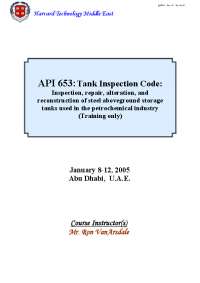
Ø A vacuum can be drawn on the box by any convenient method, such as connection to a gasoline or diesel-motor intake manifold or to an air ejector or special vacuum pump. Bubbles or foam produced by air sucked through the welded seam will indicate the presence of porosity in the seam. The vacuum box is placed over the coated section of the seam, and a vacuum is applied to the box. Ø Approximately 30 inches of the seam under test is brushed with a soap solution or linseed oil. Suitable connections, valves, and gauges should be provided. The open bottom is sealed against the tank surface by a sponge-rubber gasket. Ø Vacuum testing is conveniently performed by means of a metal testing box, 6 inches wide x 30 inches long, with a glass window in the top. Media solar, method spray, temperature ambient, holding period 4 hours. Ø The repair weld shall be visually examined for defects prior to reexamined by radiography. Ø If the resulting thickness is less than minimum required as per hydrostatic test design conditions, re-welding is required. Ø Defects shall be removed by mechanical means or thermal gouging processes. Welds that fail to meet the criteria given in paragraph above, shall be reworked prior to hydrostatic testing as follows : Ø The frequency of surface porosity in the weld does not exceed one cluster (one or more pores) in any 4 inches of length, and the diameter of each cluster does not exceed 3/32 inches. For the welds that attach nozzles, manholes, clean-out opening, and permanent attachments, no undercutting exceeds 1/64 inches. Ø The maximum acceptable undercutting is 1/64 inches of the base metal for vertical joints, and 1/32 inches maximum for horizontal joints. Ø The weld has no crater cracks or other surface cracks. Visual examinations shall be carried out during all stages of fabrication to ensure that the completed fabrication meets COMPANY satisfaction and approval with particular attention being paid to the following:Ī weld shall be acceptable by this kind of inspection if the conditions are fulfilled : Ø The out of plumbness in one shell plate (single course) shall not exceed 1/250 of the course height.

Ø The plumbness of the top of shell relative to the bottom of the shell not exceed 1/200 of the total tank height. Ø Radius measured at 1 foot above the bottom corner weld shall not exceed the following tolerance: Tolerance of peaking shall not exceed ½ inch (12.7 mm). Tolerance of peaking shall not exceed ½ inch (12.7 mm).īanding measured using a straight edge vertical sweep board 36 inch (900 mm) long. Peaking measured using a horizontal sweep board 36 inch (900 mm) long. Ø Check Ambient Condition (surface & whether). Ø Check material painting (batch no, self life, brand). Ø Check traceability (Heat No & Plate No). Ø Check dimensional (Length, Thickness, Width & Diameter). Ø Check certificate (keaslian, Heat No & Plate No). Ø Check visual (free of lamination & damage).
